Création d’une petite forge au propane
Sorry, this content is not translated in English
I try to translate most of my content, but apparently not this one (yet). If you thing this content deserve to be translated, do not hesitate to send me an email!
Il y a une paire d’années, un ami coutelier m’a permis de m’initier à la forge et à la coutellerie pendant quelques jours. Ayant toujours été fasciné par le travail des métaux, sans avoir pris le temps de découvrir réellement ces métiers, je dois dire que j’ai été sacrément emballé! Alors oui, je ne deviendrai certainement pas forgeron ou coutelier, et je n’ai pas un grand talent artistique. Mais ça n’empêche pas de s’amuser un peu et d’apprendre quelques bases de forge!
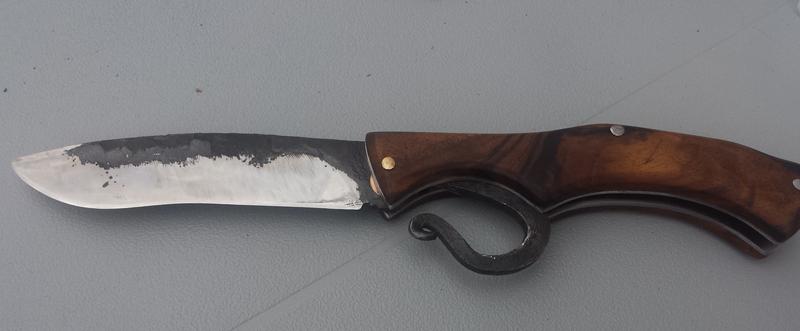
Inspirations et design général
On trouve énormément de ressources sur les Internets autour de la création de forge ou de fonderie, à gaz ou à charbon. Il s’agit presque exclusivement de vidéos, ce qui est excellent pour comprendre comment s’y prendre mais vraiment désagréable pour regarder différent designs rapidement, comparer des techniques, et surtout retrouver des informations à posteriori… J’avais déjà réalisé une petite fonderie à bois/charbon à partir d’une bouteille de gaz, me permettant corriger certains soucis que j’avais rencontré la fois précédente.
Ma première inspiration a été ce simple tutoriel sur Instructable pour la création d’une mini-fonderie à charbon. C’est un design très simple, les matériaux utilisés ne sont pas idéaux, mais ça avait au moins le mérite de rendre un peu plus concret l’idée de forge/fonderie.
Quelques vidéos très inspirantes pour les forges à gaz à partir de bouteille de butane/propane découpées :
- beau projet à deux brûleurs (en français)
- une forge assez similaire (en anglais)
L’idée générale de ces forges est simple : on prend une bouteille de gaz type butane 13kg (que l’on prend soin de bien vider préalablement!), on découpe le haut et/ou le bas du cylindre, on perce pour passer les brûleurs puis on coule du béton réfractaire autour de la paroi intérieure. Plein de variations existent autour de ce design. Par exemple, le type de porte à installer, le nombre et le système de maintient des brûleurs, l’ajout d’une couche isolante en fibre de céramique avant le béton, etc…
Pour avoir utilisé, lors de mon initiation, une forge à deux porte sur charnières verticales, j’avais envie d’avoir un système similaire la mienne. L’idée -au moins théorique- est d’ouvrir uniquement la porte avant lors d’une utilisation pour de petites pièces, mais d’avoir la possibilité d’ouvrir la porte arrière pour rentrer des pièces plus longues que l’on veut forger au milieu (au prix d’une isolation nettement diminuée et d’une montée en température plus difficile). Une autre volonté était la possibilité d’utiliser la forge comme fonderie, en fermant la porte arrière et en passant en position verticale (permettant de passer un creuset plus haut). Enfin, j’avais envie de tenter d’atteindre des températures plutôt élevées (1200°C idéalement) pour fondre des métaux plus intéressant que l’aluminium, comme du bronze, du cuivre et pourquoi pas de l’argent. Ces trois points ont guidé la conception de la forge, mais ont aussi demandé pas mal d’efforts supplémentaires. Le design final est donc un peu “trop” complexe, et rend probablement l’ensemble moins robuste. À vouloir un outil à tout faire, je vais peut-être me retrouver avec un outil que ne fait rien très bien, quoi… Bref, si vous voulez juste une forge, prenez vous moins la tête !
Un petit résumé des caractéristiques voulues pour cette petite forge :
- forge assez compacte et transportable pour aller forger à la campagne et ne pas me mettre tout le quartier à dos
- deux emplacements de brûleurs, tout en ayant la possibilité de n’en utiliser un seul (sans laisser un gros trou à la place du second…)
- porte avant et porte arrière sur charnières, avec système de verrouillage pour le transport ou pour en condamner une des deux
- posture stable horizontale (forge) ou verticale (fonderie)
- système de pieds amovible et dans une certaine mesure réglables pour mettre à niveau et rester bien stable
- deux poignées sur les côtés pour le transport
- isolation suffisante pour monter à 1200°C en mode fonderie
Brûleur à propane
La construction de brûleurs à gaz (butane/propane) est aussi très riche en ressources, avec nettement plus d’informations disponible sous forme de texte sur des sites web du début du millénaire, de forums, etc… L’objectif d’un brûleur est de créer le mélange idéal comburant/carburant (air/propane pour moi), de l’envoyer à l’intérieur de la chambre et de faciliter sa combustion.
Deux catégories de brûleurs existent : ceux à air pulsé, où une pompe est utilisée pour injecter l’air dans le mélange, ainsi que les brûleurs dits « atmosphériques » qui profitent de quelques effets physiques liés à la pression d’arrivée du gaz pour mélanger l’air sans système actif. Les brûleurs atmosphériques semblent être un peu plus délicats à équilibrer pour obtenir le ratio air/gaz désiré, mais sont évidemment beaucoup plus simple à fabriquer et ne nécessitent aucun système électrique. Plusieurs design de brûleurs atmosphériques à fabriquer soi-même se sont perfectionnés, le plus connu le brûleur « Ron Reil » dont les plans circulent depuis plus de 20 ans.
L’idée de base d’un brûleur Reil est d’utiliser de la tuyauterie en acier noir, qui résistent, sans problème à des températures de forge ou de fonderie, et dont les réducteurs (connecteurs entre tuyaux de taille différentes) sont coniques à l’intérieur. L’arrivée de gaz sous pression se fait au milieu d’un premier réducteur, dans le sens du rétrécissement, et via un tout petit trou (1mm ou mois). L’air environnant est alors entraîné par le flux de gaz à haute vitesse qui sort de ce trou, et se mélange à celui-ci dans le tube central. L’effet Venturi est exploité une première fois en provocant une accélération du mélange dans le tube central (section plus petite que l’entrée), puis une seconde fois en ralentissant le mélange à la sortie du brûleur, via une réducteur placé dans le sens inverse. Sa vitesse diminuée permet de stabiliser la flamme, et de la maintenir au niveau du réducteur de sortie (et d’éviter qu’elle se forme dans le tube, ce qui chaufferait plus notre brûleur que la chambre.
En plus d’être assez simple à réaliser, ce type de brûleur est réputé être très peu coûteux. Malheureusement, la plomberie en acier est de moins en moins utilisée, donc plus difficile à trouver et plus cher qu’il y a 20 ans, au moins en France. On peut trouver de nombreuses variantes, plus ou moins complexes à réaliser, ou en tous cas nécessitant plus ou moins d’outils d’atelier.
- une vielle réalisation un peu complexe mais très détaillée
- une alternative récente, complexe également mais bien pensée
Réalisation et test du brûleur
Le brûleur que j’ai réalisé est simple de réalisation, le matériel le plus spécifique à avoir étant des tarauds M4 et M5. Le corps du brûleur est composé d’un mamelon en acier 3/4” (20x27) de 20cm, d’un mamelon de réduction 1 1/2” femelle vers 3/4” femelle et d’un autre mamelon de réduction 1 1/4” femelle vers 3/4” femelle. Dans mon cas, j’ai substitué le premier manchon par deux manchons imbriqués : du 1 1/2” -> 1” puis 1” -> 3/4”, car la pièce n’était pas trouvable en magasin. Ce n’est pas idéal pour l’aérodynamique du brûleur, mais ça marche malgré tout.
L’arrivée de gaz dans le brûleur se fait via un tuyaux en cuivre (du 12-14), au bout duquel est brasé un bouchon en laiton. Le gaz sous pression doit passer dans le brûleur via un tout petit trou, généralement entre 0.5 et 1mm. Comme je ne suis pas très bon pour faire des trous aussi petits sans casser mes mèches, j’ai décidé de visser un embout de poste à souder MIG, qui a le bon goût de se viser sur un pas standard M4 et d’être usiné avec précision à 0.6 mm. Le bouchon est donc percé et taraudé en M4, et l’embout est vissé avec un petit bout de Téflon pour l’étanchéité. De l’autre côté du tuyau en cuivre, j’ai brasé un embout à visser 15/21, sur lequel on pourra brancher l’arrivée de gaz.
Les brasures sont réalisée à l’étain, ce qui est loin d’être idéal : les conduites de gaz doivent être jointe par brasure forte à l’argent (meilleure étanchéité et résistant à de plus haute températures). En fonctionnement normal, même la zone de l’injecteur de gaz n’atteindra pas les 200°C : le flux d’air et de gaz maintient cette partie à la température ambiante. Cependant, dès que le gaz est coupé, le flux d’air chaud venant de l’intérieur de la forge et le transfert radiatif va vite faire monter la température. Il est donc absolument nécessaire de dévisser le brûleur aussi tôt que le gaz est coupé, si la brasure est faite à l’étain ! Une brasure forte est plus que recommandée, et je reprendrai cette brasure dès que possible.
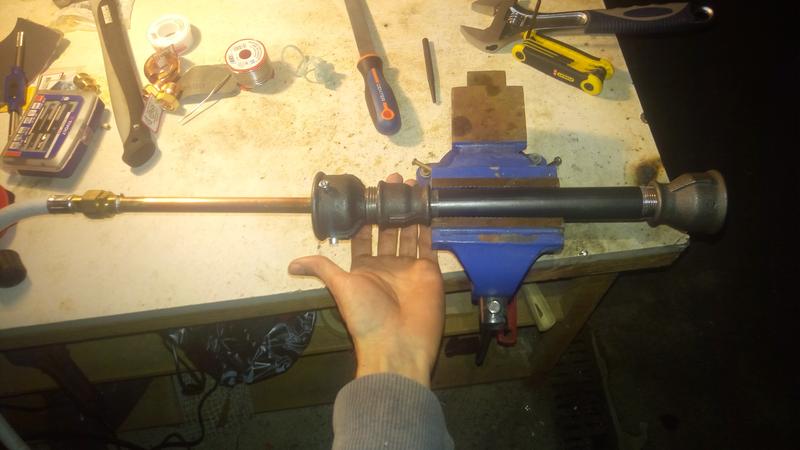
Le tuyau de cuivre est maintenu à l’intérieur du réducteur par un ensemble de 3 vis, positionnées en triangle équilatéral sur une tranche du réducteur. Il suffit donc de percer et tarauder 3 trous dans le réducteur d’entrée. Ce système permet de régler assez finement le centrage de l’arrivée de gaz et de le démonter au besoin. L’inconvénient principal est un marquage assez fort du cuivre par les vis pour bloquer suffisamment le tuyau.
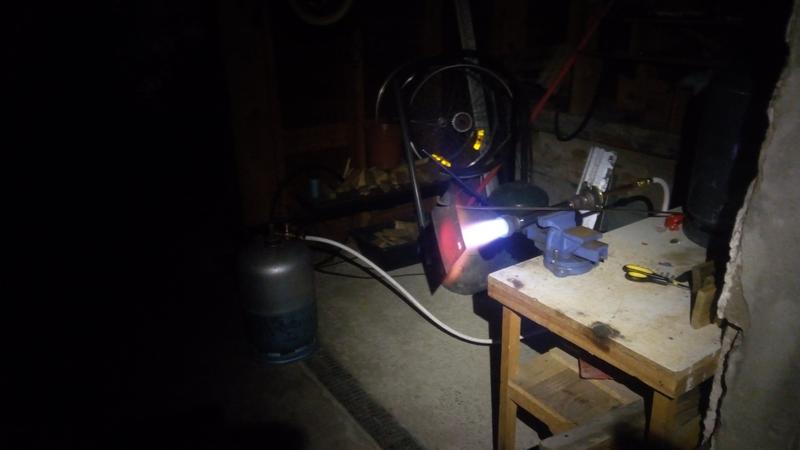
Côté bouteille de gaz, il faut un détendeur « haute pression » réglable (au moins dans la plage 0-3 bar). La gestion de la pression permettra de faire varier la puissance du brûleur et d’agir sur le mélange air/gaz en sortie. Je m’en suis procuré un avec manomètre, quasiment impossible à trouver en magasin mais disponible sur quelques sites web. Bien faire attention à la connectique des deux côtés du détendeur : dans mon cas, du 1/2 pas à gauche côté bouteille, et du M20x150 en sortie. Les flexibles de gaz habituels permettent finalement de brancher le M20x150 de sortie de la bouteille vers les embouts à visser 15/21. Moi qui n’y connais pas grand chose en plomberie, j’ai perdu pas mal de temps à comprendre toutes ces dénominations, les différents types de branchements, les matériaux à utiliser, etc…
L’un des inconvénients de ce brûleur est la difficulté d’y ajouter un mécanisme de régulation de l’entrée d’air. L’idée de ces mécanismes est de fermer plus ou moins le réducteur d’entrée pour faire varier le ratio air/gaz à la sortie du brûleur. Cette régulation est nécessaire, car une flamme trop riche en oxygène ou trop riche en carburant peut poser problème, par exemple en oxydant rapidement l’acier ou en attaquant par réduction certains oxydes du béton. Un mauvais mélange air/gaz réduit aussi l’efficacité du brûleur et peut empêcher la flamme de rester stable.
Dans mon cas, le tuyau en cuivre d’arrivée de gaz empêche de simplement placer un disque pivotant autour d’un axe sur la paroi pour faire varier l’entrée d’air. Comme cette zone est censé restée froide, j’ai confectionné un petit mécanisme en impression 3D qui va jouer ce rôle. Il est constitué d’une partie fixe, plaquée contre l’entrée du réducteur, et d’une partie mobile dont la rotation fait recouvrir ou non des trous sur la partie fixe. La conception n’est pas excellente (entre autre cela empêche d’avoir plus de 40% de l’entrée d’air ouverte), mais ça a fait l’affaire pour la fonderie et pour le premier test de la forge.
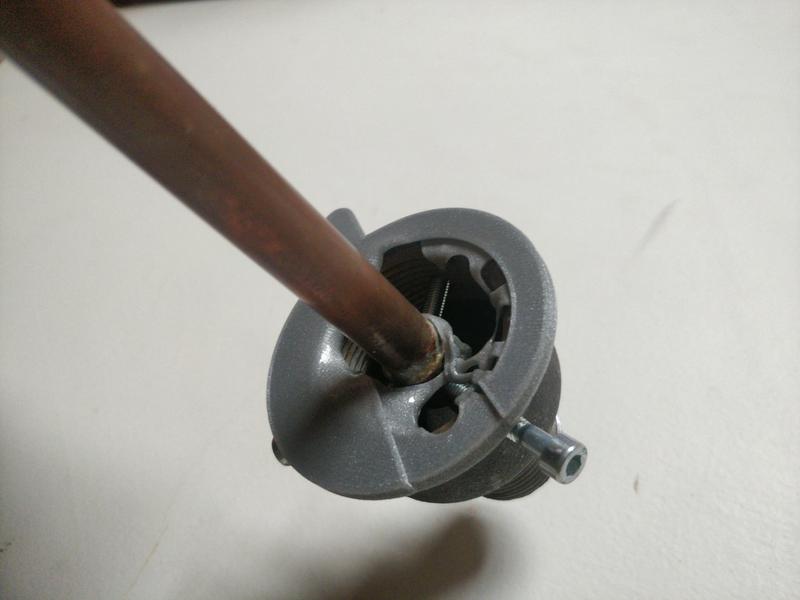
À la fin du premier démarrage de la forge, le plastique (PETG) a fondu avant que je n’ai le temps de dévisser le brûleur. La position quasiment verticale du brûleur sur la forge est beaucoup plus problématique que la position horizontale sur la fonderie : dès que le gaz est coupé, la chaleur remonte dans le tuyau. J’ai donc fait un nouveau système de fermeture sur un axe soudé au bord du réducteur, avec une découpe en arc de cercle pour faire passer le tuyau d’arrivée du gaz. Comme je n’ai pas de bons outils pour découper ce passage, ça a été une ébauche à la meuleuse et beaucoup de temps à la lime.
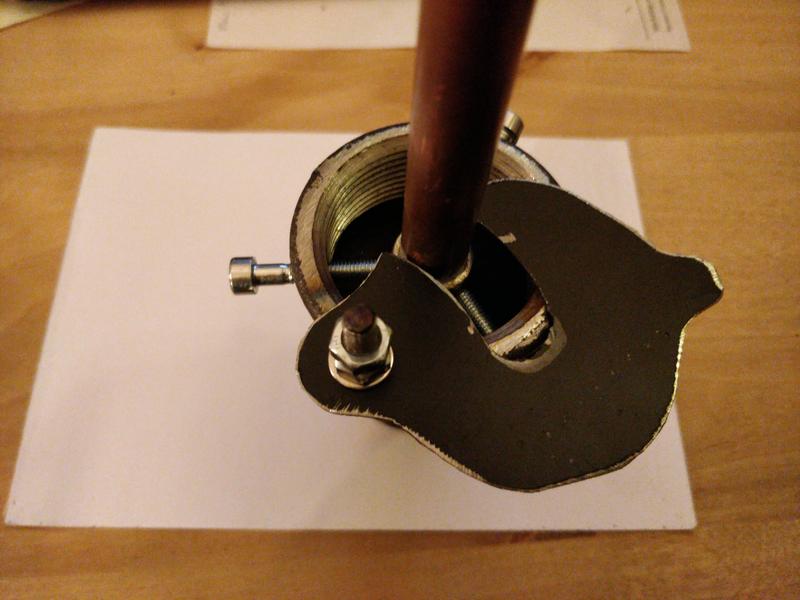
Réalisation de la forge
La réalisation de la forge elle-même m’a pris pas mal de temps, bien plus que prévu, certainement par ce que j’ai très peu d’expérience en soudure à l’arc (ça se voit très bien à l’aspect des soudures, je sais qu’elles sont très crades) et en usinage des métaux en général. J’ai aussi pas mal improvisé au fur et à mesure, et j’ai essayé d’utiliser le plus de matériaux de récupération ou que j’avais en stock, d’où quelques mauvais choix qui m’ont coûtés une après-midi ou deux…
Préparation de la bouteille de gaz
On parle ici de découper des containers de produits hautement inflammables !
Les bouteilles doivent être vidées correctement avant toute découpe, et le conseil habituel
est de s’assurer d’un remplissage à l’eau et d’un vidage quelques jours après avant de découper
quoi que ce soit.
Cette bouteille m’a posé quelques soucis, et j’ai agi de manière potentiellement risquée, mais
je vous conseille d’être plus prudent (mieux vaut une heure de perdue que le visage brûlé)…
Quelques bouteilles standards de 13kg traînaient dans la cours, et m’ont déjà servies pour d’autres projets. Celle-ci était la dernière du lot, pour une raison simple : je n’ai pas réussi à dévisser le bouchon (malgré un outil créé pour ça avec un bras de levier de 1m50 quand même…) ! Après avoir fait de mon mieux pour la vider avec le bouchon, en la laissant ouverte pendant plusieurs semaines et en pompant de l’air à l’intérieur de temps en temps, j’ai décidé de couper le bouchon tranquillement à la scie à métaux. Une fois tranché, l’accès est plus direct et j’ai pu remplir patiemment la bouteille avec de l’eau pour chasser le reste de gaz.
On commence par découper à la meuleuse de chaque côté pour créer les deux portes et libérer le cylindre qui formera le cœur de la forge. Un premier point complexe pour moi est l’installation des charnières. Je commence par la porte « avant », avec des charnières clairement sous-dimensionnées qui traînaient dans ma visserie. Pour rendre les choses plus simples, je décide judicieusement d’utiliser de la taule d’environs 1mm d’épaisseur comme support, ce qui me permettra de galèrer avec mon poste à souder et de pester sur la flexibilité de l’ensemble… Comme je veux pouvoir démonter les portes, je décide de relier les deux parties avec 3 petits écrous reliant une plaque soudée aux charnières et l’autre soudée sur le corps de la forge.
Toute la charnière me prend pas mal de temps à cause des opérations assez délicates : découpe et meulage de la taule pour avoir la forme de la section à souder, soudure entre deux pièces très fines (charnière et taule) et ajustement des deux plans pour que le couvercle se ferme bien. Bref, le résultat est assez moche, mais étonnamment fonctionnel. Les soudures font peur mais sont finalement assez résistantes. Un léger jeu est présent quand on porte du poids sur la porte, qui est attribuable aux charnières et pour une moindre mesure à la finesse de la taule. De l’autre côté, je soude un système de fermeture assez basique que j’avais probablement démonté d’un meuble. Il permettra de maintenir la porte fermée si nécessaire, pour maintenir au chaud des pièces après avoir coupé le gaz ou pour déplacer la forge par exemple.
Pour la seconde charnière, le résultat est catastrophique. Je pense avoir appris de mes erreurs, et donc j’utilise une grosse charnière que j’avais en réserve, dans un acier plus épais. Le tout est soudé sur le corps de la forge, et se visse côté porte dans des trous que j’ai taraudé, à l’intérieur d’un fer plat épais qui est lui-même soudé. Le système semble robuste et les soudures plus faciles à réaliser (on est plus sur de la taule de 1 mm… ). Par contre, l’utilisation d’une seule charnière, bien que plus épaisse, était une énorme connerie. Le jeu sur l’axe d’ouverture est très important, ce qui rend difficile la fermeture de la porte et réduit nettement la confiance dans la solidité de l’ensemble…
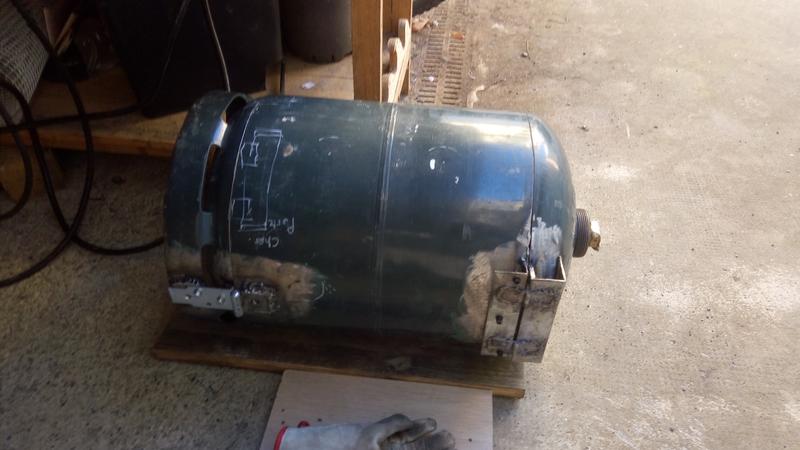
Après avoir passé autant de temps sur deux malheureuses charnières, je laisse ça de côté et je reviendrai plus tard arranger le problème. Un coup de meuleuse pour virer toute trace de l’échec précédent, deux charnières intermédiaires et du fer plat de 4mm rendent le tout bien plus stable ! À noter que j’ai garder l’ancien système de fixation côté porte tel quel, mais qu’il mériterait d’être étendu en haut et en bas pour rigidifier la fixation.
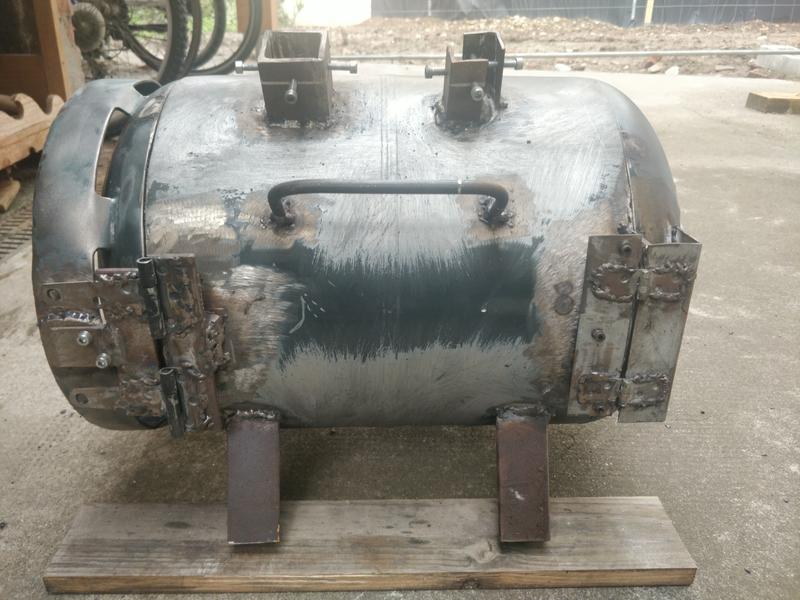
Je passe ensuite au perçage des entrées des brûleurs à l’aide d’un trépan métal. Les entrées ne sont pas parfaitement symétriques, pour rendre le brûleur avant un peu plus proche du milieu de la forge si je n’utilise qu’un seul brûleur. Le perçage s’est révélé assez délicat, en particulier à cause de la section cylindrique qui empêche d’être bien à plat sur toute la surface des dents du trépan. J’ai réussi à bien abîmer les dents (au moins 3 qui ont cassé, d’autres qui sont émoussées) mais au moins j’ai mes trous !
Pour maintenir le brûleur en place, je pensais souder un bout de tube cylindrique de gros diamètre avec 4 trous taraudés pour bloquer le brûleur avec des vis. Comme je n’avais rien sous là main avec un diamètre suffisant, j’ai fait avec les moyens du bord : deux bouts de cornières soudées et taraudées. Entre la fabrication des deux brûleurs, j’ai trouvé une cornière plus longue et plus épaisse qui permet de faire un passage un peu plus propre.
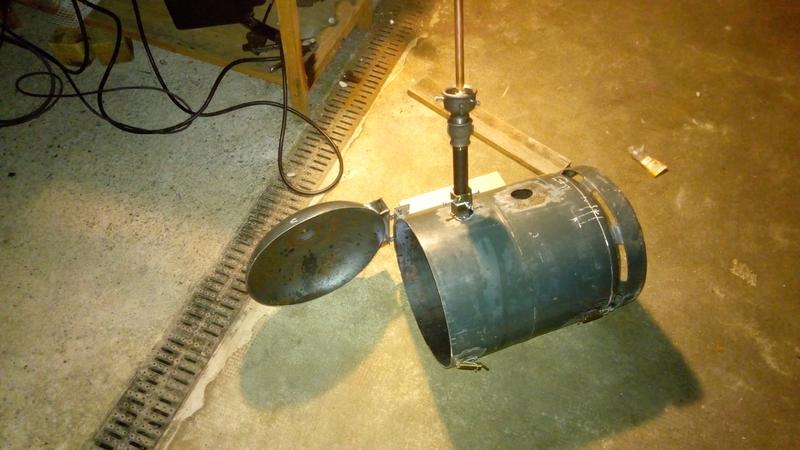
Pour poser la forge, mon objectif était d’avoir 4 pieds amovibles, et si possible ajustables pour se mettre bien droit même sur un terrain pas idéal. Des supports (bouts de cornières assez épaisses) vont donc être soudés, dépassant d’une dizaine de centimètres et les pieds à proprement parler pourront être boulonnés dessus. Pour cela, je commence par souder 4 supports le long du cylindre après avoir marqué le bas de la forge. Cette opération était bien plus complexe pour moi que je ne l’avais anticipé : les pieds doivent avoir le même angle dans la mesure du possible, sur les trois axes. Mais comme je n’ai aucune surface plane comme référence, je suis obligé de faire une sorte de gabarit en plastique transparent pour avoir au moins une base. Le tout en tenant à la main les supports le temps de pointer au poste à souder…
Après avoir soudé les 4 pieds, je me rend compte que l’un d’eux est trop incliné, il faudra sûrement que je meule au moins un côté pour le rectifier et le re-souder. Plus compliqué à régler par contre : le plan vertical que j’avais tracé comme référence est décalé de plusieurs degrés, par rapport aux plan des charnières. Pas vraiment de solution autre que meuler les pieds et recommencer, je ferai avec en sur-élevant les pieds d’un côté.
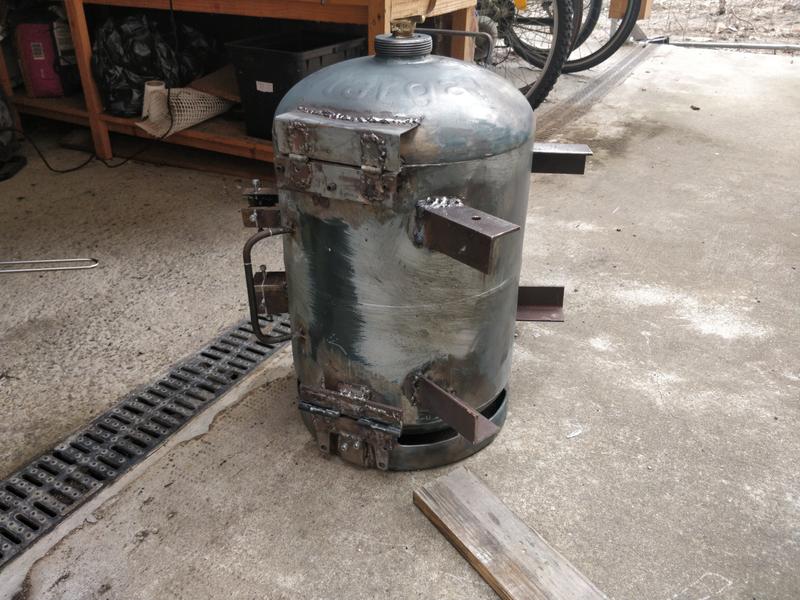
Comme la forge va peser une 40aine de kilos, j’ajoute deux poignées que je forme en cintrant avec mon étaux et un tube fin qui traînait. Les poignées sont placées légèrement sur le dessus de la forge, j’ai l’impression que ce sera plus pratique et moins encombrant comme ça.
À ce stade, j’ai à peu près toutes les fonctionnalités que je voulais sur la carcasse de la forge. Il resterai à placer une poignée sur chaque porte, mais je perd un peu patience, et je met ça de côté comme finition une fois la chape de béton réfractaire coulée. Par contre je commence à m’inquiéter du maintient en place du béton. Sur la fonderie que j’avais réalisé, j’ai eu le droit à un démoulage impromptu du béton que j’avais coulé dans le couvercle : il n’avait pas bien accroché aux parois et avec les différences de températures a fini par simplement se décrocher, sans même se fissurer avant…
L’idéal serait d’armer le béton et de l’ancrer à la structure en métal. Malheureusement, il est très déconseillé d’armer du béton réfractaire de manière traditionnelle. Les coefficients de dilatation entre de l’acier standard et le béton sont trop différents à ces températures, et il y a plus de chances de fragiliser la structure que de la renforcer ainsi. Il existe bien des aciers réfractaires conçus pour ça, mais c’est un budget à ajouter et ce n’est pas simple pour un particulier d’y avoir accès. Après avoir tourné un peu en rond, je fini par décider de faire un ancrage minimum : 2 bouts de fer à béton de chaque côté du corps de forge, et 2 autres sur chaque porte. Ça me semble très léger, mais j’ai un peu peur d’en mettre plus. Les bouts sont un peu tordus pour éviter un bête glissement si une fissure apparaît autour des ancres.
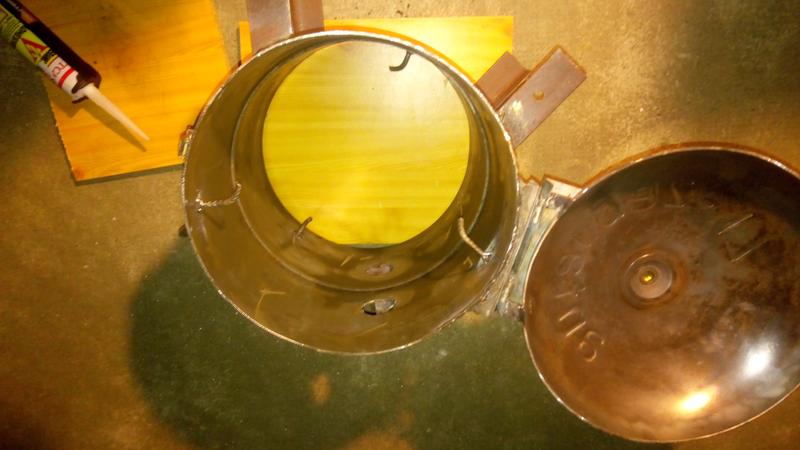
Installation du revêtement en fibre de céramique
Les fibres de céramiques sont des fibres minérales très similaires à l’amiante.
Elles sont depuis plusieurs années considérées cancérigènes
pour des raisons similaires (fibres se logeant dans les voies respiratoires).
Si vous en utilisez, vérifiez les équipements de protection adéquats, au stricte minimum un masque
FFP3 durant les découpes et la manipulation des fibres.
Il est fortement déconseillé de laisser des fibres de céramiques sans revêtement de surface, comme je l’ai
fait la porte arrière.
Maintenant que la carcasse est à peu près terminée et avant de couler le béton, j’installe la laine de céramique autour des parois et au fond des portes. La laine est donnée pour 2.5cm d’épaisseur, mais je suppose que ça compte une partie de tassement avec un produit durcissant puisque je mesure plutôt 4cm sans écrasement. Cette fibre se découpe assez facilement avec un simple cutter. Je prépare donc un rectangle à enrouler dans le corps de la forge et deux cercles à plaquer au fond de chaque porte.
Une fois découpé, j’applique un mastic haute température fourni par le même fabriquant le long des parois et je plaque la fibre contre le mastic. Comme pour tous ses produits, je n’ai trouvé aucun manuel technique précisant les caractéristiques du mastique, les temps et conditions de séchages ou les procédures d’applications. Il faut se contenter de trois lignes sur le site web et deux lignes d’information directement sur le produit…
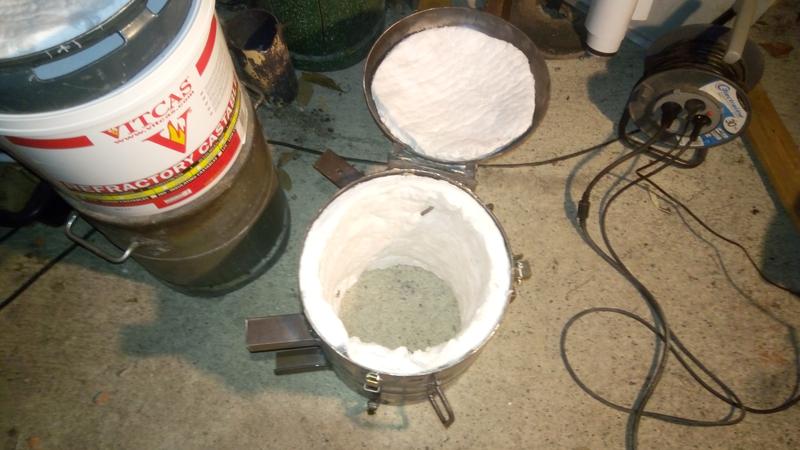
Peu après, j’applique un rigidifiant de fibre céramique. Aucune information sur le procédé d’application et de séchage non plus, j’imite donc ce que j’ai pu voir à droite et à gauche sur les Internets… L’application se fait au pinceau, en y allant assez franchement pour imbiber correctement la fibre. Après avoir attendu 24h, la laine est toujours molle en surface. À priori, ce type de rigidifiant est simplement une solution de silice très fine dans de l’eau. Je suppose donc qu’il faut au minimum faire évaporer l’eau, et idéalement fondre la silice au chalumeau. Le peu d’information que j’avais trouvé jusque là me faisait penser qu’une simple application et un séchage à l’air seraient suffisant, ce processus est beaucoup plus long que prévu et je suis un peu inquiet d’endommager la fibre en chauffant trop la surface.
Coulage du béton réfractaire
Ça commence à ressembler à une forge! Plus qu’à couler le béton réfractaire autour de la fibre. Le béton est indiqué pour 1600°C, sûrement un ciment à haute teneur en alumine (pour les curieux, le diagramme de phase alumine-silice aide à comprendre un peu la composition des réfractaires). Son but est :
- de fournir une protection haute température à la fibre de céramique, en évitant que le brûleur ne fasse fondre la partie des fibres exposée à la flamme
- apporter une petite inertie thermique à la forge
- augmenter un peu l’isolation, même si à épaisseur égale la laine semble à peu près 10 fois moins conductrice de chaleur
L’inertie thermique est plus souvent considérée comme un inconvénients que comme un avantage. Mais vu les dimensions de cette forge, et du brûleur, un peu d’inertie devrait aider à avoir une température plus uniforme et plus facilement contrôlable. Et tant pis si ça implique de chauffer une 30aine de kilo de béton en plus…
Pour couler la paroi, je prépare un coffrage improvisé qui formera le cylindre intérieur. Il est constitué de deux conserves de collectivités (diamètre ~13cm), épaissi par 2 tours de tapis de sol en mousse et lissé par un tour de textile plastifié, le tout atteignant un diamètre d’à peu près 18cm. Bref, du grand art, mais mis à part quelques déformations à prévoir je m’attend à ce que le coffrage ne soit pas trop mauvais. Il faut aussi anticiper les trous pour les brûleurs. Je bricole un coffrage de dimension similaire pour le second emplacement de brûleur, à partir d’un tube en acier entouré de mousse de matelas de sol. Les deux éléments sont placés dans la position désirée pour les brûleurs, maintenu par les vis de blocage. La forge est finalement mise en position verticale, sur une planche, et le coffrage intérieur est maintenu dans sa position par quelques bouts de gaffer. Un pistolet à colle aurait permis d’avoir un coffrage plus propre, mais j’utilise ce que j’ai sous la main.
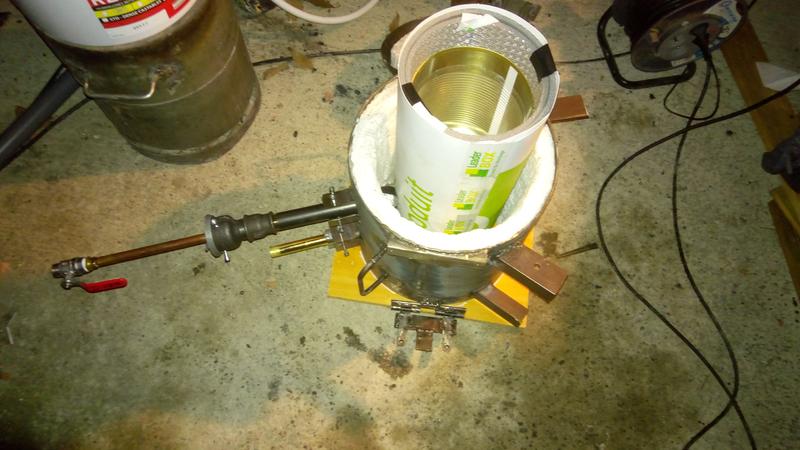
La préparation du béton me laisse perplexe. Il est vendu comme un béton relativement liquide, pour des coffrage et des moulage de pièces, mais la proportion d’eau à ajouter (2L pour 25kg) parvient à peine à rendre la pâte humide. Malgré les risques de fragilisassions du béton, je suis obligé de rajouter bien plus d’eau, autour de 3.5L pour 25kg. Une fois le coffrage rempli, en tassant au fur et à mesure avec une tige en métal, je prépare les portes pour couler le béton au dessus de la laine de céramique.
Mon calcul de quantité de béton nécessaire pour le volume à couler étant, comme d’habitude, sous-estimé, je suis obligé d’improviser pour la deuxième porte. J’utilise donc un mortier réfractaire qu’il me reste, donné pour 1300°C, pour la tapisser la porte arrière.
En essayant d’imaginer un système de fermeture efficace de la porte arrière, je voulais appliquer un cordon de fibre de céramique pour garder une relative étanchéité aux flammes et limiter les pertes en utilisation fonderie (position verticale). J’ai donc découpé un morceau de corde en fibre de céramique (diamètre 20mm), que j’ai enfoncé délicatement dans le béton à environs la moitié de sa hauteur. Avec du recul, l’idée semble plutôt mauvaise, surtout que j’ai placé les fibres bien trop à l’intérieur, les laissant exposées directement au fond du four… Bref, ça risque surtout de me filer un cancer et les fibre vont certainement fondre au fur et à mesure, mais il faut bien faire des erreurs.
Plus qu’à attendre 24h pour décoffrer et le plus longtemps possible pour que le béton rigidifie correctement (idéalement, au moins 3 semaines, et les propriétés mécaniques s’améliorent encore après ça). Au moment du décoffrage, le béton est encore très fragile, probablement à cause de l’excès d’eau dans le mélange. J’en profite pour gratter quelques endroits où le béton est en excès, en particulier au niveau des brûleurs.
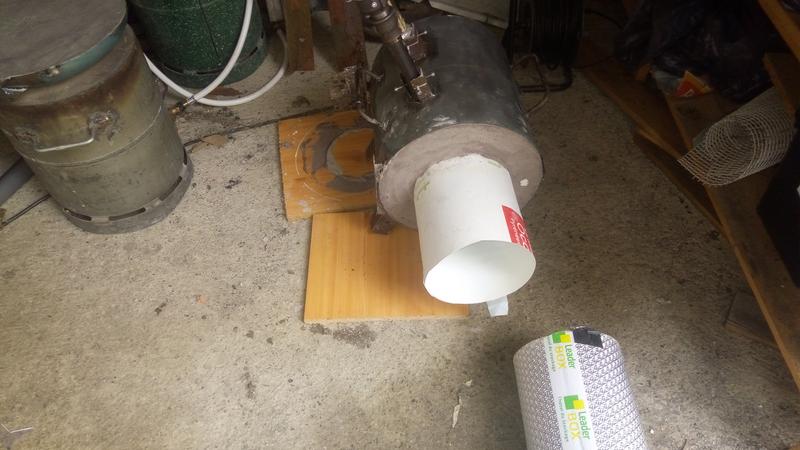
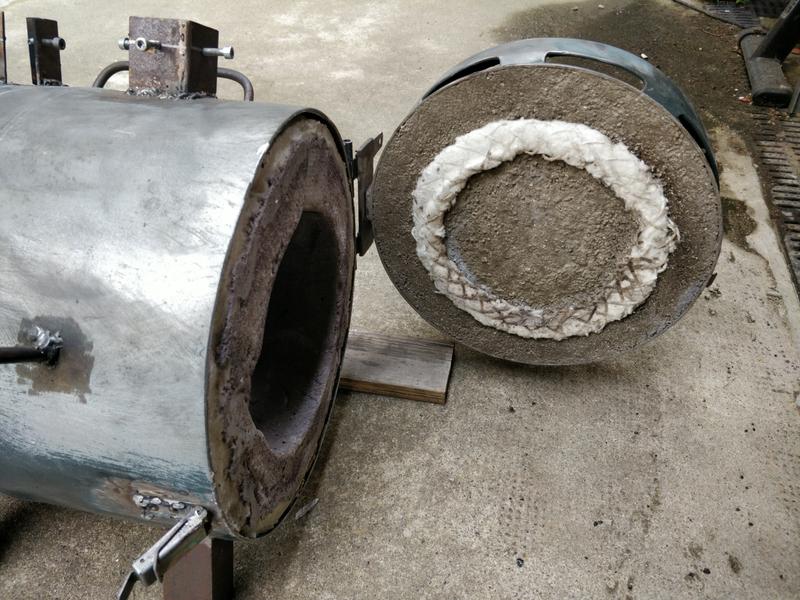
Après quelques jours, je prépare la dernière partie en béton : une petite dalle à insérer dans le corps de forge, pour avoir une zone à plat que l’on peut retirer en utilisation verticale pour la fonderie. Cette pièce va aussi être la partie la plus exposée aux flammes des brûleurs, et je m’attend à ce qu’elle s’abîme très vite. Mais si ça peut limiter un peu l’usure de la paroi, ce sera toujours moins compliqué d’en refaire une que de tout re-couler.
La technique est un peu ridicule : un simple film alimentaire en cellophane posé au fond du cylindre intérieur de la forge. Un peu galère à placer comme rien n’adhère au béton, mais j’arrive à peu près à ce que je veux. Au dernier moment, je me décide à insérer un bout de fer à béton dans la dalle, qui risque de se casser sur sa grande longueur sans renfort. On verra aussi à quel point l’idée d’armer du béton réfractaire soumis à plus de 1000°C est une mauvaise idée ! Après 3 jours de prise, j’enlève cette pièce en béton pour la faire sécher à côté.
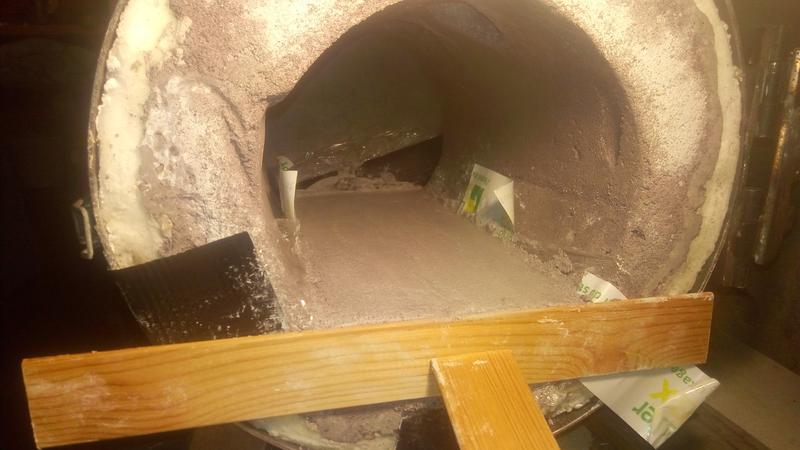
La petite touche finale : Black is the new Black
Pour protéger un peu l’acier de l’oxydation, mais surtout pour un petit plaisir esthétique, j’ai passé un petit coup de peinture en spray résistante à la chaleur. Deux ou trois couches suivant les endroits, sans trop de prise de tête. Le résultat est très satisfaisant1 !
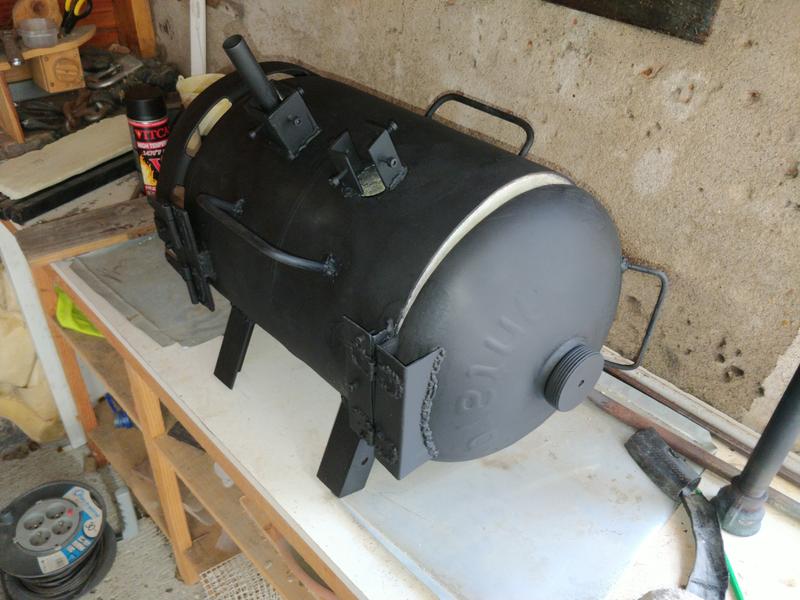
Premiers essais
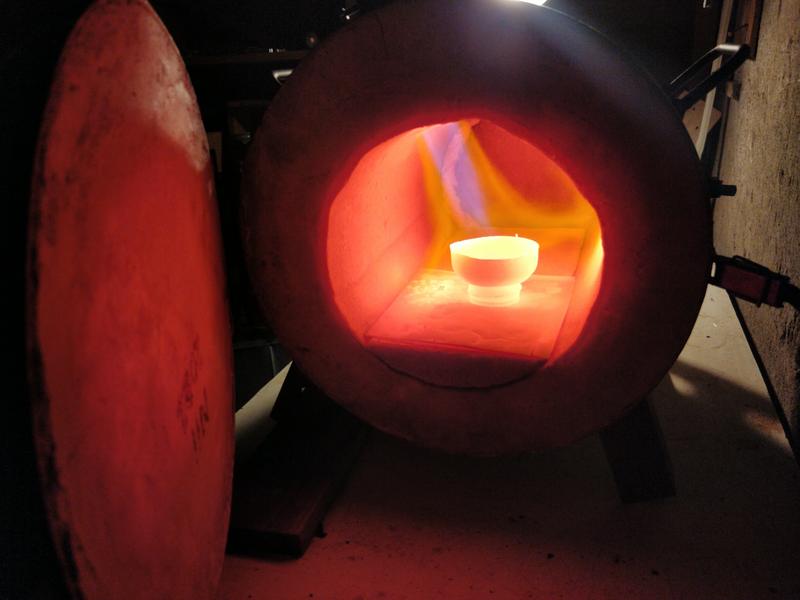
Après 2 semaines de séchage, j’ai fini par perdre un peu patience et j’ai allumé la forge. Une semaine de séchage supplémentaire aurait certainement été préférable pour avoir une dureté optimale du béton. Le premier allumage est critique, car c’est là qu’on va chasser l’humidité résiduelle du béton. Si la chauffe est trop rapide, la faible porosité du béton ne va pas être en mesure d’évacuer la vapeur assez vite, et la pression va faire fissurer le béton. Il faut donc y aller progressivement, sur plusieurs heures, pour limiter le plus possible la fissuration.
Une partie l’humidité est simplement de l’eau « libre » qui est piégée dans la structure du béton, et qui va se vaporiser à 100°C. Cependant, une autre partie de l’eau est chimiquement liée à d’autres molécules du béton, formant différents hydrates. Chacun de ces hydrates va perdre sa molécule d’eau à une température bien spécifique, entre 200°C et 500°C d’après les quelques informations que j’ai pu glaner. Comme je n’ai pas de four industriel à commande numérique pour faire une belle montée de la température uniforme et avec des palliers aux bons moments, on va juste essayer de prendre un peu de temps.
La durée totale de ce premier allumage a été d’environs 4h. J’ai commencé par allumer le brûleur avec une pression très faible (environs 0.3 bar) pendant quelques minutes, en prenant soin de placer une plaque d’acier sous la flamme du brûleur pour limiter le point chaud. Cette étape est répétée 3 fois en laissant quelques minutes de répit pour que la température se diffuse et s’équilibre un peu. Ensuite, le gaz est maintenu en continu, en augmentant progressivement le débit, jusqu’à une pression maximale de 2 bars au bout d’environs 2h30. Pendant toute cette durée, de la vapeur se dégage de la forge, se frayant un chemin via la fibre de céramique et les quelques trous existant entre le béton et la paroi métallique. J’ai eu tendance à me baser sur la quantité de vapeur pour réguler le débit, en augmentant la flamme dès que la quantité de vapeur visible devenait assez faible.
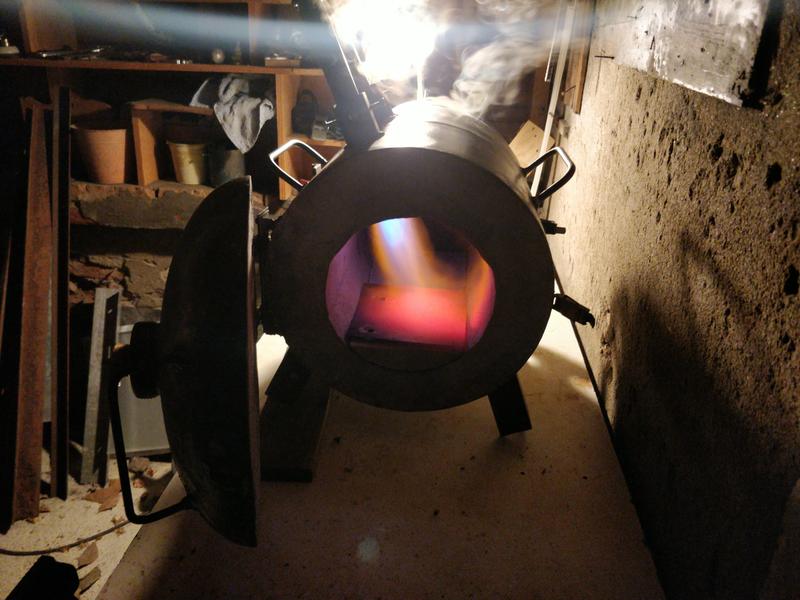
À la fin de ce premier feu, la température dans la forge est comprise entre 1000°C au fond et plus de 1250°C sous la flamme, d’après mon thermomètre infrarouge J’en ai profité pour faire fondre un petit bout de cuivre qui traînait sur l’atelier, ce qui est assez réjouissant ! Après quoi je coupe le gaz, je dévisse rapidement la partie supérieur du brûleur (mais pas assez rapidement pour le régulateur d’air en plastique visiblement) et je laisse la forge refroidir lentement avec les deux portes pratiquement fermées. La masse thermique est assez importante (plus de 25kg de béton quand même), mais l’isolation semble aussi bien meilleure que dans la fonderie, qui ne possède pas la paroi en fibre de céramique. Près de 20 minutes après avoir coupé le brûleur, l’intérieur est encore à près de 800°C, et il sera encore au delà des 300°C au bout de 4 heures. Il faudra malgré tout voir si la laine de céramique est utile sur des sessions plus courtes de chauffe, ou si au contraire l’inertie thermique du béton limite son intérêt.
La première fissure est apparue assez vite pendant la chauffe, à l’avant sur le haut de la voûte. Sachant qu’elle est sur une zone où la laine de céramique est très proche, ça ne me semble pas trop inquiétant au départ. Après avoir refroidit, la fissure semble s’être propagée jusqu’à trou du brûleur avant, et tout le haut de la voûte semble fragilisé. Quelques petites fissures plus petites sont apparues au refroidissement, sur la porte arrière et sur les bords de l’ouverture avant, mais ne sont pas préoccupantes pour l’instant. Même si elles ne mettent pas la forge en péril actuellement, ces fissures vont rendre la forge beaucoup plus délicate à transporter et à manipuler de manière générale. Il faudra un peu plus de recul pour savoir à quel point ces premières fissures vont impacter la durée de vie du revêtement…
Rétrospective
Cet article est déjà assez long, mais je voudrai prendre un peu de recul sur la réalisation de la forge, histoire d’aider de futurs bricoleurs à se lancer dans ce type de projet.
Coûts et matériel
La réalisation d’une forge à gaz n’est pas nécessairement très coûteuse. On doit pouvoir s’en sortir pour environs 100€, brûleur compris, en utilisant un mortier réfractaire moins performant trouvable en magasin de bricolage (indiqué pour 1300°C au moins) et en faisant un peu de récup’ pour les poignées et autres petites pièces d’acier. Dans mon cas, j’ai dépensé nettement plus, et je vais essayer de détailler un peu ce qui a coûté cher et pourquoi.
Déjà, j’ai voulu utiliser des matériaux assez techniques (laine de céramique et béton réfractaire donné pour 1600°C). Cela oblige à commander à des fournisseurs assez spécifiques, et j’ai acheté des produits annexes dont j’aurais pu me passer, comme le rigidifiant pour la laine de céramique (faisable soi même pour beaucoup moins cher), du mastic spécial laine de céramique (du mortier réfractaire aurait fait le même boulot), de la corde en fibre de céramique (que j’ai utilisé maladroitement et qui laisse de la fibre de céramique potentiellement cancérigène exposée)… Et malgré les matériaux utilisés, il est probable que la forge se détériore en quelques dizaines d’utilisations : même le meilleur béton réfractaire fini par fissurer avec les différents chocs thermiques auxquels on l’expose dans une mini-forge.
Ensuite, j’ai acheté beaucoup de petits éléments que j’aurais pu récupérer dans des chutes industrielles ou sur des meubles abandonnés. Quelques bouts de fer plat, des vis, boulons, rond en acier pour les poignées, quelques charnières, la visserie pour les tuyaux de gaz… Il y a moyen de faire autrement si vous avez un budget très serré.
Pour certains éléments, j’ai fait le choix d’acheter dans des magasins physiques, pour pouvoir manipuler un peu les objets avant l’achat ou pour continuer d’avancer le jour même. Pour certaines pièces, la différence de prix avec des sites de vente en ligne est vraiment énorme, par exemple la tuyauterie en fonte noire utilisée pour le brûleur. Le tout est trouvable pour moins de 20€ en ligne, mais j’ai dû payer autour de 45€ en magasin, et après avoir fait le tour de 3 magasins de quincaillerie pro autour de chez moi.
Enfin, le coût global inclus aussi des achats de matériel finalement inutilisé (pas mal de robinetterie en laiton que je pensais utiliser avant de changer de plan par exemple) et d’outils achetés pour la réalisation du projet. Bien sûr, les outils serviront, je l’espère, à plein d’autres choses et le matériel inutilisé dépannera sur un autre projet à l’avenir. Mais ces deux catégories comprennent une grosse partie du budget, et je vous conseille de l’anticiper si vous vous lancez dans un projet similaire.
Élément | Prix | Alternative |
---|---|---|
Détendeur haute pression réglable avec manomètre | 40€ | Détendeur sans manomètre |
Béton réfractaire 1600°C, 25kg | 47€ | Simple mortier réfractaire |
Rigidifiant pour fibre céramique | 47€ | Pas de fibre céramique |
Laine en fibre de céramique 25mm, 3m | 45€ | Pas de fibre, 1m seulement est suffisant |
Colle pour fibre de céramique | 15€ | Peut-être juste un peu de béton réfractaire? |
Corde isolante en fibre de céramique 20mm, 2m | 10€ | Ne rien mettre? |
Peinture thermorésistante | 10€ | Ne pas peindre |
Robinetterie en fonte noir pour brûleur (voir détails) | 40€ | Sites web beaucoup moins chers |
Tuyauterie laiton et cuivre pour le gaz (voir détails) | 50€ | Éviter d’acheter plein de pièces inutiles… |
Petite ferronnerie (fer plat, charnières, rond d’acier…) | 40€ | Faisable en récupération |
Total approximatif | 344€ |
Une petite liste non exhaustive des outils utilisés :
- poste à souder à arc MMA (électrode enrobée)
- meuleuse d’angle (disques à meuler et à tronçonner)
- lampe à souder à gaz de plombier
- perceuse
- forets métal
- trepan métal 40mm
- tarauds M4, M5 et M6
- et tout plein de petit outillage commun (limes, équerre, serre-joint, pointeau, règle droite, etc…)
Conseils pour une future réalisation
Si je me relance dans un autre projet de forge à gaz, il y a certainement quelques enseignements que je retirerai de cette réalisation. En espérant que ça puisse aiguiller d’autres gens, voilà quelques points importants pour moi.
Hybride forge/fonderie
L’idée de vouloir utiliser le même dispositif comme forge et comme fonderie n’est pas forcément une mauvaise idée, mais a posé pas mal de soucis et je risque finalement de ne l’utiliser pratiquement que pour de la forge. La bascule en position verticale (permettant de faire rentrer un creuset imposant) est finalement assez difficile, à cause du poids de l’ensemble. Les fissures le long de la voûte en béton ne donnent pas trop envie de secouer l’ensemble… La position du brûleur est aussi peu adaptée à l’utilisation en fonderie : le brûleur est dirigé directement vers le centre de la cavité, alors qu’il est préférable de l’orienter presque à la tangente de la section cylindrique pour diffuser au mieux la chaleur dans une petite fonderie. Enfin, l’idée d’avoir un jour au fond de la fonderie (au niveau de la porte arrière pour l’utilisation horizontale) ne me rassure pas du tout. En cas de trou dans un creuset, je préfère savoir le métal fondu contenu dans le béton plutôt que de risquer de le voir couler à l’extérieur…
Cette conception « double usage » m’a aussi forcé à faire une dalle amovible pour avoir une surface plane dans le bas de la forge. En plus de la complexité ajoutée par la création de la dalle, la surface montre déjà des signes de fatigue après seulement quelques utilisations…
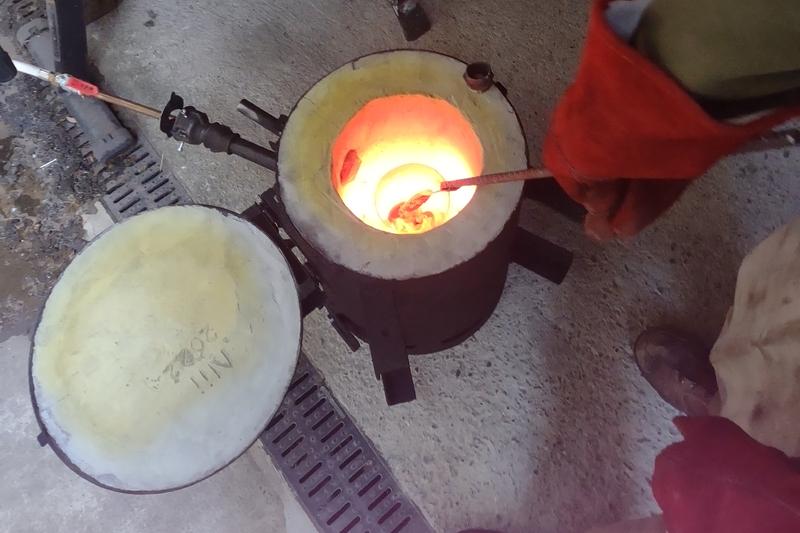
Double porte avant/arrière
Le fait d’avoir une porte à l’avant et à l’arrière (idée tirée de la forge de mon ami) est vraiment chouette. Sur les quelques sessions de forge, j’ai eu plusieurs fois des objets un peu longs à passer, qui sans l’ouverture arrière auraient été plus complexes voir simplement impossibles à forger. Évidemment la chaleur dans la forge réduit dès qu’on maintient la porte arrière ouverte, mais ça semble être un moindre mal.
Une amélioration sympathique serait d’avoir un accès plus petit sur la partie avant. Pas mal de forges à gaz maison sont conçues avec une petite ouverture, autour de 10cm x 10cm, ce qui permet de passer des petits objets sans perdre trop de chaleur. Pour de la coutellerie par exemple, ouvrir complètement la porte avant ne semble pas très optimal. L’idéal aurait été de découper un accès sur la porte avant, simplement bloqué par une taule en acier amovible par exemple.
Fibre réfractaire et béton
L’isolation de la chambre est peut-être à revoir. Avec les épaisseurs que j’ai mis, il me semble que l’isolation est vraiment satisfaisante mais l’inertie thermique semble plutôt élevée. Quitte à mettre des fibres de céramique, il est peut-être préférable d’en faire une épaisseur plus importante (2 couches de nappe ?) et de réduire l’épaisseur du béton. Ou alors ne pas mettre du tout de fibre réfractaire et accepter une inertie thermique très importante. Tout dépend évidemment de l’usage : si l’objectif est de travailler des petites pièces occasionnellement, les quelques minutes d’attente pour que le béton chauffe risques de consommer beaucoup de carburant !
-
Même si ça ne cachera jamais les soudures très… expérimentales ! ↩